Exploring the Diverse Applications of HDPE Pipe Welder
Exploring the Diverse Applications of HDPE Pipe Welder
In the realm of modern engineering, HDPE pipe welders play a pivotal role in shaping the infrastructure that sustains our cities, supporting agricultural practices, and driving the mining industry. This article delves into the multifaceted applications of HDPE pipe welders, from urban development to rural irrigation and mining projects, highlighting their significance and impact.
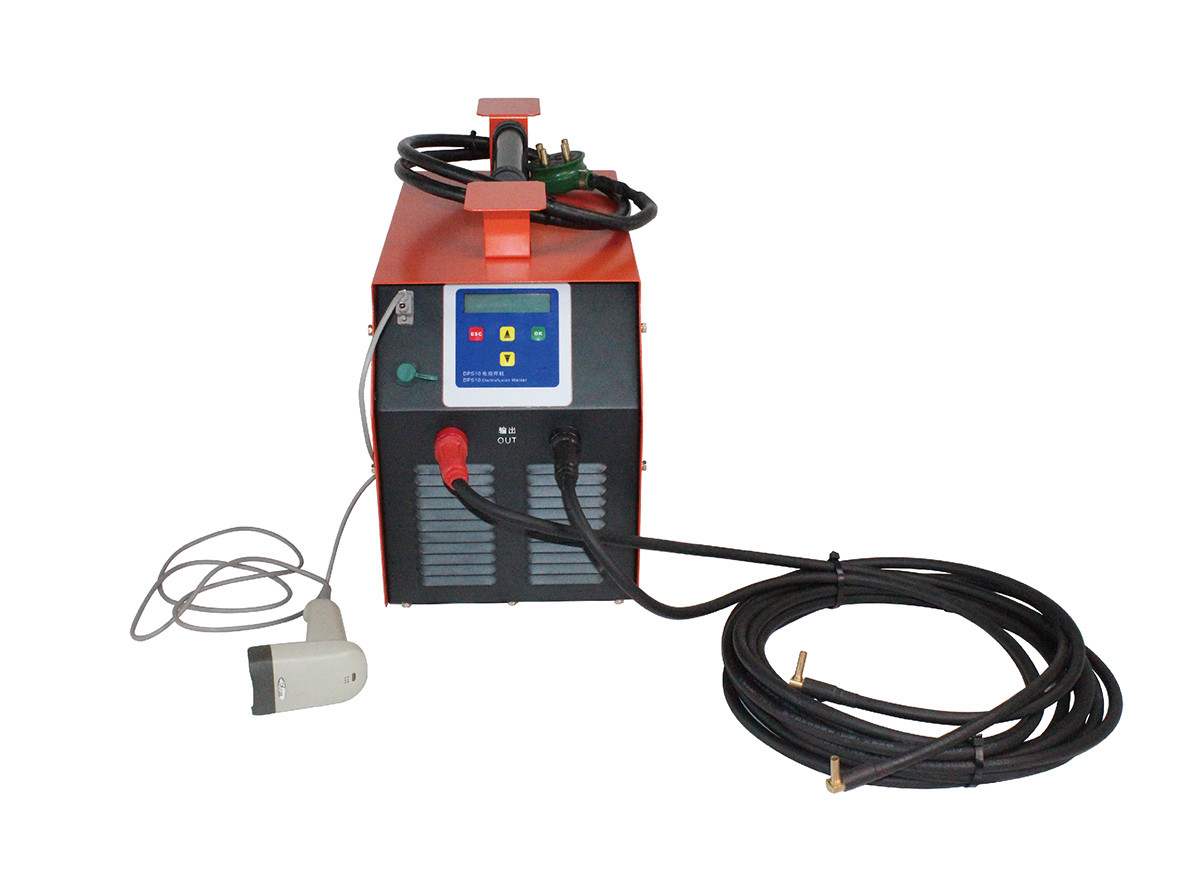
In the realm of urban construction and municipal projects, HDPE pipe welders take center stage. They are the driving force behind the seamless connections of drainage systems, gas pipelines, and the emerging networks of renewable energy conduits. From the swift and secure socket fusion method to the precision of electrofusion, these machines ensure reliable joints, minimizing leaks and ensuring the longevity of vital urban systems.
**Application Example:** In a bustling metropolis, electrofusion welding creates gas distribution networks that power homes and businesses, ensuring a continuous supply of energy while reducing environmental impact.
II. Agricultural Irrigation Advancements:
Turning our attention to agriculture, HDPE pipe welders revolutionize irrigation practices. By efficiently joining pipes for water distribution, these machines contribute to water conservation and efficient resource utilization. Whether it's the butt fusion technique for mainline connections or the socket fusion method for lateral lines, HDPE welders enable farmers to optimize irrigation systems, enhancing crop yields and conserving precious water resources.
Example: In a vast agricultural expanse, socket fusion welding forms the backbone of drip irrigation systems, delivering water directly to plant roots and maximizing water efficiency.
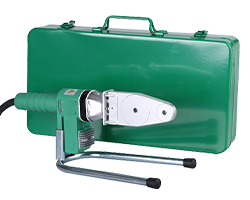
III. Powering Mining Projects with Strength and Precision:
HDPE pipe welders are instrumental in the mining sector, where the demands for high-strength, high-performance joints are paramount. Whether it's the challenge of creating reliable tailings disposal systems or durable slurry transport pipelines, butt fusion welding technology ensures that these critical components withstand the rigors of mining operations. The precision of these welders also guarantees leak-free connections, minimizing environmental impact.
Example: Deep within a mine, butt fusion welding secures slurry transport pipelines, maintaining a seamless flow of materials critical to the mining process while upholding environmental standards.
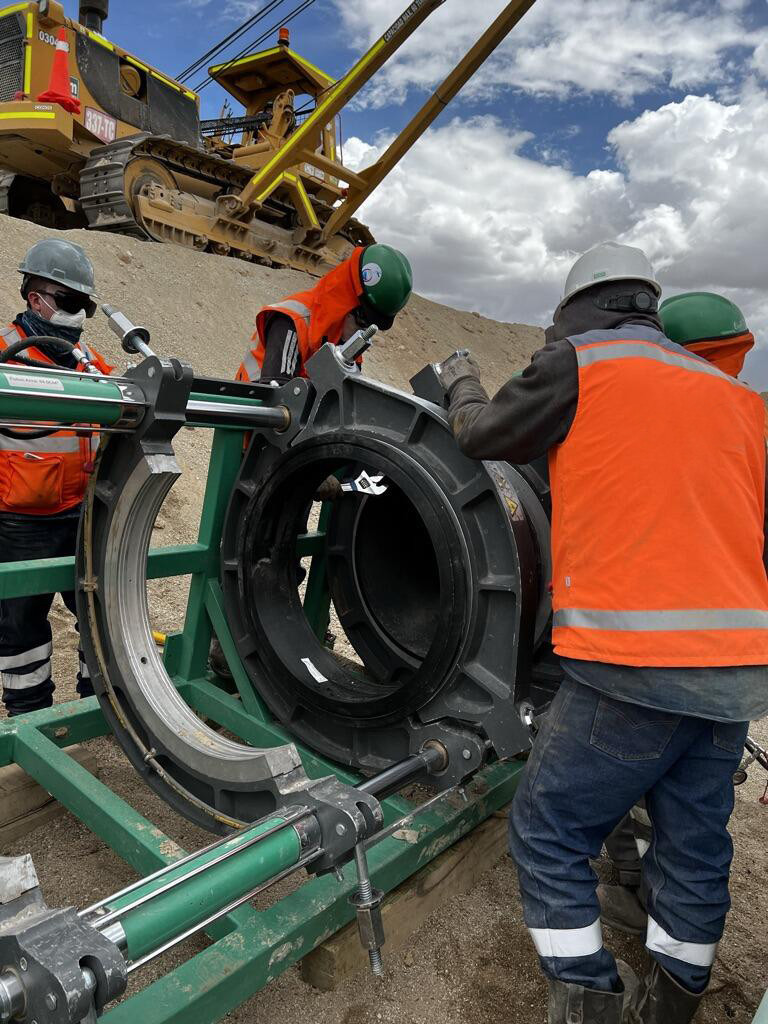
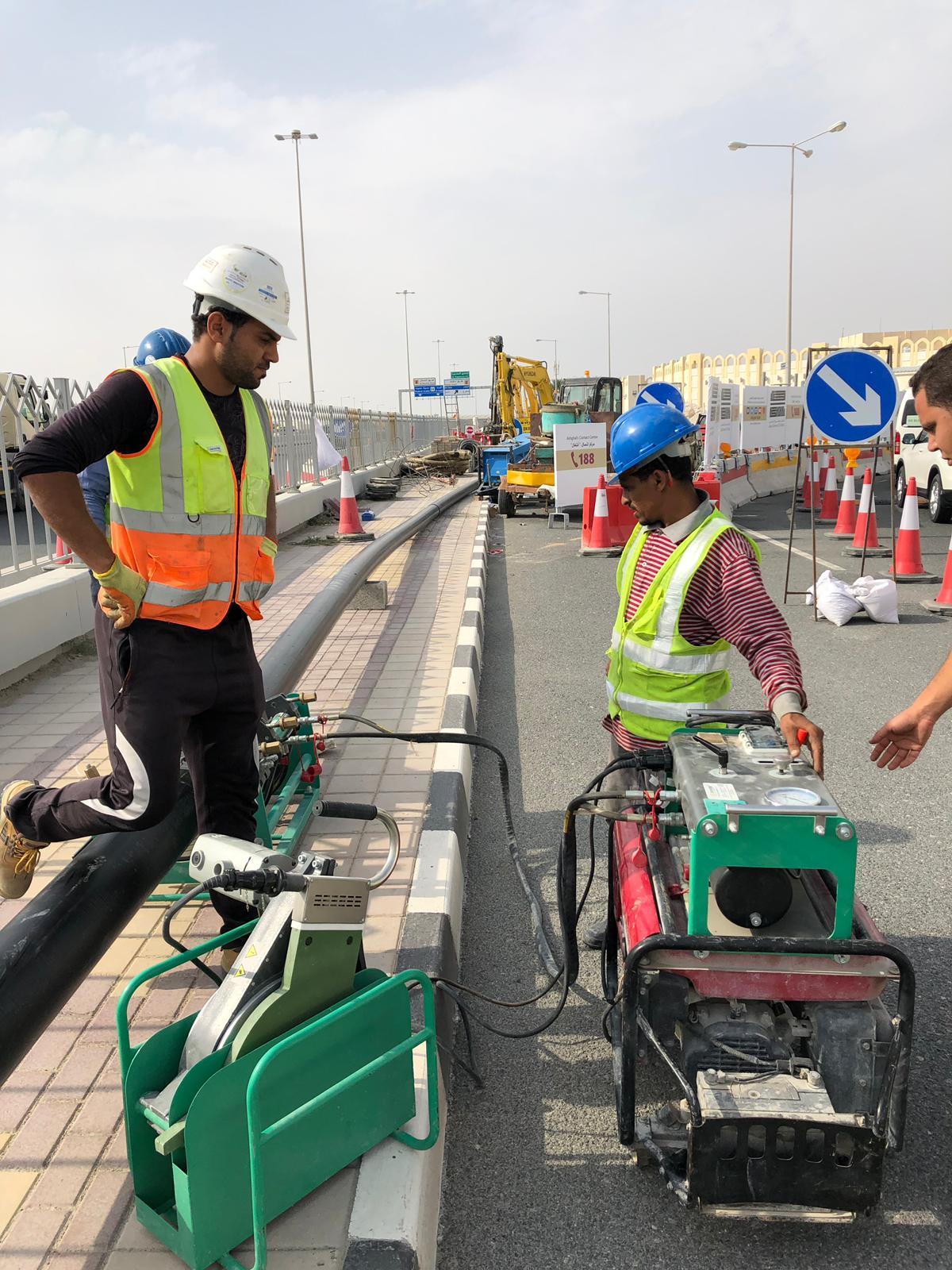
IV. The Confluence of Fusion Techniques:
The versatility of HDPE pipe welders lies in their ability to adapt to different fusion techniques, each with its unique applications.
- Socket Fusion: Ideal for smaller diameter pipes and intricate joints, socket fusion welding finds its place in projects requiring precision and compact connections.
- Electro Fusion: Employed in gas distribution networks and water supply systems, electrofusion welding ensures secure joints for critical utilities, minimizing leakage risks.
- Butt Fusion: Well-suited for larger pipes and straight joints, butt fusion welding shines in projects demanding high structural integrity and hydraulic performance.
Conclusion: Pioneering the Future with HDPE Welders:
As we traverse the landscape of urban growth, agricultural development, and mining endeavors, HDPE pipe welders stand as silent heroes, shaping the core of modern society. From the bustling cities to the serene fields and beneath the earth's surface, these machines create connections that power progress, sustain livelihoods, and uphold environmental responsibility. The fusion of innovation and technology paves the way for a future built on the reliability and strength of HDPE pipe welders.